Unknown Facts About Alcast Company
Unknown Facts About Alcast Company
Blog Article
Little Known Questions About Alcast Company.
Table of ContentsThe 9-Minute Rule for Alcast CompanyThe Greatest Guide To Alcast CompanyHow Alcast Company can Save You Time, Stress, and Money.Not known Facts About Alcast CompanyThe Facts About Alcast Company UncoveredThe Ultimate Guide To Alcast Company
The refined distinction lies in the chemical material. Chemical Comparison of Cast Aluminum Alloys Silicon promotes castability by lowering the alloy's melting temperature and improving fluidness throughout spreading. It plays a crucial role in enabling detailed molds to be filled up properly. Additionally, silicon adds to the alloy's strength and put on resistance, making it important in applications where sturdiness is vital, such as vehicle parts and engine components.It additionally boosts the machinability of the alloy, making it less complicated to refine into ended up items. By doing this, iron adds to the total workability of aluminum alloys. Copper raises electrical conductivity, making it useful in electrical applications. It also enhances corrosion resistance and includes in the alloy's overall toughness.
Manganese adds to the toughness of light weight aluminum alloys and improves workability. Magnesium is a lightweight component that provides toughness and effect resistance to aluminum alloys.
Some Ideas on Alcast Company You Should Know
Zinc improves the castability of light weight aluminum alloys and helps manage the solidification procedure during casting. It enhances the alloy's toughness and firmness.
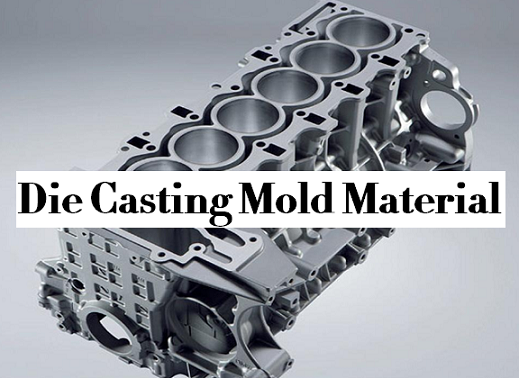
The main thermal conductivity, tensile toughness, yield toughness, and elongation differ. Among the above alloys, A356 has the highest possible thermal conductivity, and A380 and ADC12 have the cheapest.
The Basic Principles Of Alcast Company

In precision spreading, 6063 is well-suited for applications where complex geometries and high-grade surface coatings are paramount. Instances include telecommunication units, where the alloy's exceptional formability enables streamlined and aesthetically pleasing layouts while maintaining architectural stability. In the Lights Solutions sector, precision-cast 6063 components create sophisticated and effective lighting fixtures that need complex forms and good thermal performance.
The A360 shows premium prolongation, making it optimal for complicated and thin-walled components. In accuracy spreading applications, A360 is appropriate for sectors such as Customer Electronics, Telecommunication, and Power Devices.
The Facts About Alcast Company Uncovered
Its distinct properties make A360 a useful option for accuracy casting in these sectors, improving product durability and top quality. Light weight aluminum alloy 380, or A380, is a commonly used spreading alloy with several distinctive qualities. It provides excellent castability, making it a suitable option for accuracy casting. A380 displays excellent fluidity when molten, guaranteeing intricate and thorough molds are accurately duplicated.
In accuracy casting, aluminum 413 shines in the Customer Electronic Devices and Power Equipment industries. This alloy's remarkable corrosion resistance makes it an excellent choice for outdoor applications, ensuring long-lasting, resilient products in the recommended you read stated industries.
Some Of Alcast Company
The aluminum alloy you choose will substantially influence both the spreading procedure and the buildings of the final product. Because of this, you have to make your decision carefully and take an enlightened strategy.
Identifying the most suitable aluminum alloy for your application will certainly imply considering a broad variety of attributes. These relative alloy attributes follow the North American Pass Away Casting Organization's guidelines, and we've divided them into 2 groups. The very first group addresses alloy features that influence the production process. The second covers characteristics affecting the properties of the final item.
Alcast Company Can Be Fun For Everyone
The alloy you choose for die spreading straight affects numerous facets of the casting procedure, like how simple the alloy is to collaborate with and if it is susceptible to casting flaws. Warm fracturing, additionally referred to as solidification cracking, is a regular die casting defect for aluminum alloys that can cause interior or surface-level tears or splits.
Certain light weight aluminum alloys are much more at risk to hot fracturing than others, and your choice should consider this. One more common problem discovered in the die spreading of aluminum is pass away soldering, which is when the cast sticks to the die walls and makes ejection hard. It can harm both the cast and the die, so you ought to try to find alloys with high anti-soldering buildings.
Corrosion resistance, which is already a significant feature of light weight aluminum, can differ substantially from alloy to alloy and is an essential characteristic to consider depending on the environmental conditions your product will be subjected to (aluminum foundry). Put on resistance is an additional residential or commercial property typically sought in aluminum products and can distinguish some alloys
Report this page